迪元仪表精益生产之路
- 2017/5/17 14:23:28 13045
- 来源:仪表网
会议现场,公司副总经理孙向东作题为“为智慧工厂提供迪元智慧”的报告,全面介绍了迪元仪表的概况和企业发展历程,深入阐述了迪元仪表在智能水表和智能流量计等产品的开发、生产、销售及技术服务领域的优势。
迪元仪表致力于工业自动化过程控制领域智能流量仪表开发、生产、销售和技术服务,是参与制定七项国家和行业标准的高新技术企业,属于中石化、中石油和中海油物资供应商成员单位。
在企业24年发展过程中,通过逐步凝练并不断调整和提升,建立了基于传统文化并植入现代元素具有迪元特色的企业文化,形成了“敬天爱人·自利利他”的核心价值观理念。公司实施绩效管理模式,把创新工作放在首位,以打造流量仪表品牌为目标,不断推出技术的高科技产品,提升公司的品牌形象和市场竞争力,员工绩效与企业业绩得到显着提升。近年来,每年销售额均达亿元,新产品所占比重均超过80%。
自2010年以来,公司逐步呈现出订单交期达成率下降、成本增加、库存加大的趋势。为了完成订单生产任务,产线工人加班加点,但效率始终不如人意,问题症结究竟在哪里?2013年3月,通过邀请日本丰田工程技术株式会社崛切俊雄社长来改善进行现场诊断,现场管理、品质、物流、标准作业、生产管理等方面的管理水平较低构成制约订单交付的重要因素。为此迪元仪表于2013年8月导入TPS,开始向精益生产转型。2014年定制开发MES生产管理系统,进一步提升生产管理效率,提高公司的经济效益。
精益生产是以消除浪费、降低成本为目的,以准时化和自动化为支柱,以改善活动为基础,通过消除所有环节上的浪费来缩短产品从生产到客户手中时间从而提升企业竞争力的生产方式。为了向精益生产转型,公司成立了5S、QC、物流、生管、作业五个改善小组,从示范线开始逐步推行至各工序,经历了几度热情、痛苦、快乐的周转过程,改善整个理念始终贯彻在TPS推行全程,从“革新”到“革心”,员工思想受到震撼心灵得到洗礼。
现场5S改善是精益生产的基础,标准化作业改善、工序内物流改善、品质提升均是以5S为基础开展,在5S改善过程中,运用《5S检查表》,对照现场进行评分,同时查找存在的问题并制定相应对策,采用《问题改善管理表》进行改善的跟踪管理,透过全员点点滴滴的改善,使得现场干净整洁、物品定置管理、目视化水平提高,并终形成5S标准。
品质改善通过现场查找收集质量问题,运用QC七大手法,对问题进行汇总分析,查找问题发生的真因,并制定有效对策加以实施。通过编制QC工程表、品质检查标准书,各工序开展首末件检验,产品质量在各工序内得到了保证。
物流改善通过如仓库的目视化、安全库存设置、工序间搬运设计调查、多频次少量化采购、流程再造、线边库设置、现品票与材料卡的运用等措施,对库存管理、采购流程与方式、工序流程、生产计划优化等方面进行改善。
通过现场观察记录员工的作业顺序,发现作业过程存在的7大浪费现象,列入浪费发现调查表,编制标准作业票,运用作业改善的方法,分析如何减少各种浪费,并实施改善。
随着精益生产方式的应用,新的问题随着出现。精益生产看板管理需要的大量各种票据、数据表格,依靠人工管理、手工排程已不能满足管理需求,公司2014年开始定制开发MES生产管理系统,对BOM、订单拆分、库存、采购、制程排单、产能平衡、在制品、产成品、报工等方面进行电脑管理,自动生成现品票、材料卡等,用以规范管理生产全过程。
通过精益生产方式的应用,零件加工过程的合格率由98.7%提高99.3%,工序间搬运时间减少10%以上,总库存降低13.8%,交期达成率提升29%达到88%。
推行TPS的目的在于通过改善,改变员工原有的思想观念和习惯。通过全员改善,减少乃至消除现场的各种浪费,优化流程,提高公司管理水平和生产效率,同时培养和挖掘一大批管理人员。
改善是永远的、无限的,改善没有终点,通过持续推行TPS,优化不足,朝着精益生产的道路不断迈进,为实现迪元“打造流量仪表品牌”的美好愿景而努力!
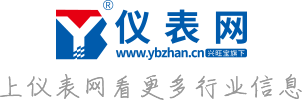
全部评论